In a breakthrough for sustainable construction, Scottish cleantech company Kenoteq is poised to make a global impact with a revolutionary product designed to tackle one of the building industry’s most pressing challenges: waste.
The company, a spinout from Heriot-Watt University, has developed the K-BRIQ, a construction brick composed of nearly 100% recycled materials, primarily construction and demolition waste that would otherwise end up in landfill. Now, after years of rigorous testing, the K-BRIQ has achieved official certification from the British Board of Agrément (BBA), one of the UK’s most respected bodies for validating construction products.
This milestone positions Kenoteq’s innovation as not just an eco-friendly alternative, but a viable, certified solution that can now be specified with confidence across UK building projects—from public infrastructure to private developments.
“This certification marks the arrival of a truly transformative building material for the construction and interior design industries,” said Dr Sam Chapman, Co-founder and Executive Director of Kenoteq. “It allows us to scale with confidence, and signals to developers, architects, and policymakers that sustainable alternatives are ready for mainstream use.”
The environmental credentials of the K-BRIQ are staggering. Unlike traditional clay-fired bricks, which require high temperatures and energy-intensive processes, the K-BRIQ is unfired, cutting carbon emissions by up to 95% during production. For a standard two-bedroom house using 12,000 bricks, switching to K-BRIQs could reduce CO₂ emissions from over 5 tonnes to just 0.2 tonnes, equivalent to taking a petrol car off the road for an entire year.
Beyond reducing emissions, the K-BRIQ tackles another urgent problem: the mountain of construction waste clogging landfills worldwide. In the UK alone, construction, demolition, and excavation waste accounts for over 60% of total waste, around 50 to 60 million tonnes each year. Globally, construction debris is estimated to make up more than a third of all landfill material.
Kenoteq’s model offers a bold alternative. Using construction waste as raw material, the company is able to manufacture new bricks within 24 hours of waste arriving at its low-energy production facility in East Lothian, a closed-loop model that is both fast and sustainable.
With production capacity currently at 2 million bricks per year, and infrastructure in place to scale to 4 million, Kenoteq is gearing up to meet growing demand as sustainable construction practices become an industry imperative.
The path to BBA certification was far from conventional. With no standard testing framework for non-traditional bricks made from recycled materials, Kenoteq’s product underwent years of intensive testing, including thermal performance, structural integrity, water resistance, and fire safety. The K-BRIQ not only passed these tests, it excelled.
The product received the maximum durability rating possible, a critical benchmark for the UK’s variable climate. Additionally, its Medero Dark Grey variant achieved an A-class fire safety rating, qualifying it for use in high-risk buildings.
“Securing BBA certification allows our product to be specified with confidence on commercial projects across the UK,” Chapman explained. “We’ve already seen strong interest from major developers, architects, and public sector bodies who are under pressure to reduce carbon footprints and build sustainably.”
The certification also satisfies critical regulatory and insurance requirements, overcoming a key hurdle that has historically slowed the adoption of innovative materials in the built environment.
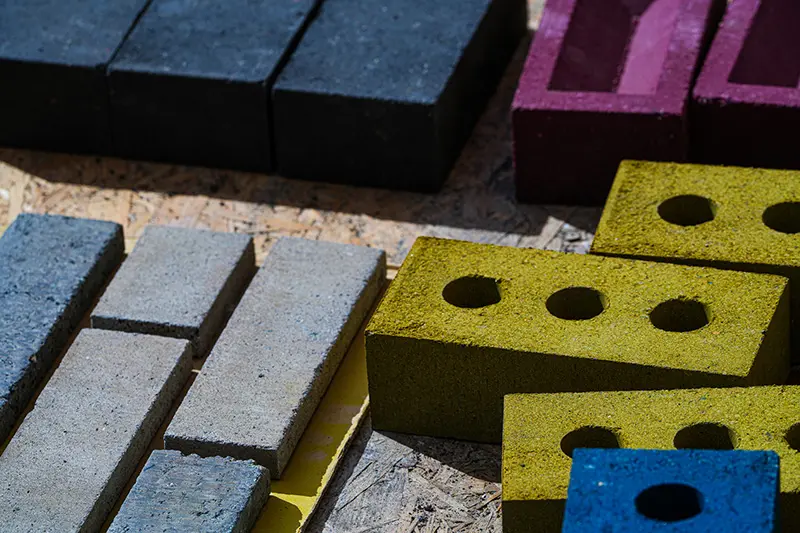
Kenoteq’s ambitions don’t stop at UK borders. The K-BRIQ recently received parallel certification in the United States via the DrJ Technical Evaluation Report (TER), and European certification is currently underway. Inquiries from international partners are already streaming in, positioning this Scottish startup at the forefront of a global movement toward circular construction.
“The K-BRIQ is not just a greener brick, it’s a technically robust, aesthetically flexible material ready for a wide range of applications,” said Chapman. “It meets the same performance standards as traditional materials but with a fraction of the environmental impact.”
Available in 12 colours, thanks to recycled pigments the K-BRIQ offers architects design flexibility without sacrificing sustainability. Its use in both exterior façades and interior features opens the door for widespread application in residential, commercial, and civic buildings.
K-BRIQs have already been used in high-profile demonstration projects, including installations at Scotland’s National Retrofit Centre (BE-ST), Oaklands College in St Albans, and a Kaufland sustainability flagship store in Germany. The bricks are also featured in a growing number of Gail’s Bakery locations across the UK.
Public sector organisations and climate-conscious developers in cities like London are eyeing the product as a tool for meeting net-zero targets and improving environmental performance on large-scale projects. Educational institutions and urban regeneration schemes are also expected to lead in adoption.
“We are proud to support clients like Kenoteq in bringing innovative, sustainable solutions to market,” said Katy Roberts, Sales and Marketing Director at the British Board of Agrément. “In construction, trust and performance are non-negotiable and third-party certification plays a key role in enabling innovation to flourish.”
With more than 2.5 billion bricks used in the UK each year and over 500 million imported, many from outside the EU, the environmental cost of traditional brick making is immense. The K-BRIQ represents a tangible solution, turning construction waste into construction value, and shifting the industry toward a circular economy.
As the building sector faces mounting pressure to decarbonise and reduce its footprint, Kenoteq’s innovation offers a compelling path forward, one built brick by recycled brick.